Chemical Inventory: Item and Organizational Operations
Regulatory Aspects
Chemicals that are on a specific list, need to determine which apply to your organization and what type of information and/or data do you need to know and possibly extract about your inventory. This can be in the form of complying with specific items such as CFATS, volume related reporting such as Tier II, geography such as local or state requirements such as Prop 65 for the state of California, traits of the chemicals such as radioactive isotopes or communications such as if a chemical is hazardous and access to safety data sheets (SDSs).
Determine what regulations will apply to you and information that you need gather and report. In order to gather data it’s important to understand how the item moves throughout and interacts with your organization.
Product Movement
In short, we want to understand how an item is requested, tracked, arrives, placed in inventory, used and exits. Each organization differs, but here are details to consider in each of these steps.
Requests can be from companies (ordering) or from other labs both internal and external. What documents are need when items are arrive from an external lab?
Tracking after the request is made, who is responsible for ensuring the item arrives? How often should they monitor this process? How and with who should they communicate cancellations or delays?
Arrival, are items delivered to a loading dock, temporary inventory or directly to labs?
Who accepts packages? Does the package need to have a PO or other details to be accepted? How is the requestor notified that the item has arrived? Is this person responsible for looking for damages to the item, incorrect item or missing number of units?
Place item in inventory, does the lab record that the item has arrived? Does the item need to be barcoded, tagged or recorded? How are documents stored related to the item such as SDSs or user manuals?
Exit, how are items leaving your facility? What items can recycled or disposed of in normal trash? What items need special care such as sharps, bio-hazard or hazmat handling?
In general there are two broad examples, centralized which companies tend to follow and branched which is more popular in academics.
Centralized
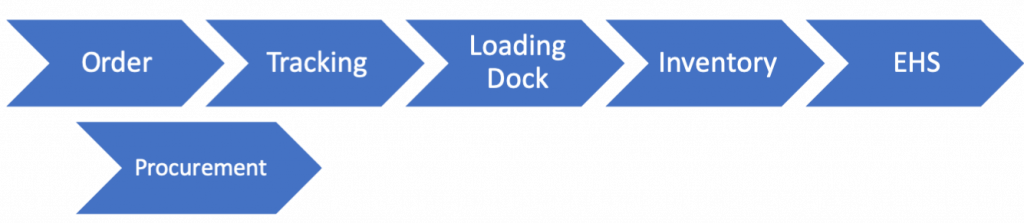
Decentralized
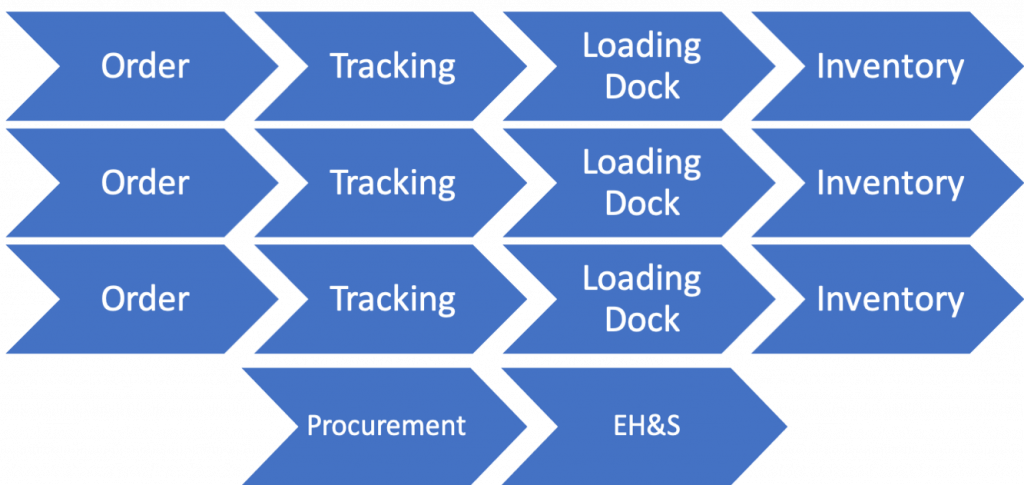
Your particular system will likely be hybrid with certain parts being centralized (procurement and EHS) and others (ordering and item locations) branched. In universities it is common to have a more decentralized workflow with each lab ordering, tracking and monitoring their inventory. The labs may share a loading dock if their within the same building, but systems need to account for different workflows.
Organizational Workflow
Once we have a good grasp of how the item moves through the facility that will give us guidance on the human element such as departmental considerations:
Environmental Heath and Safety (EH&S) will be focused on regulatory aspects as mentioned, but also risk management. What hazards do you have on site, how to move gas cylinders properly, hazards that may develop such as peroxide formers or how much flammable liquids do you have on a given floor?
Research and Development may want to know location of products to know where items are located to streamline efficiency.
Manufacturing can be concerned with on site inventory to maintain production levels.
Procurement has an interest in idle inventory, duplicate orders, pricing and better value in both price and service.
There are more examples, but the underlying consideration is who will need to access the inventory system and what information needs to be entered and extracted from it.
Scope
Do all departments and their stakeholders need to be involved for a comprehensive solution? Is it for one lab, building, institution wide? What is the scope of implementation such as number of chemicals and to how handle different facilities?
How are we going to manage kits, propriety solutions and creating compounds? Do we need to inventory all chemicals or only HAZMAT items?
Roles and Responsibilities
Who is doing what?
Compliance, who is responsible with entering the data, less people makes this process much easier. How often will audits be done to ensure the inventory is accurate?
Permissions, who can view, edit and extract data from the system and which parts? Who is in charge of assigning permissions?
Software and Tools
The exciting part and often where companies start, please don’t start here, try to get a plan together first. It will help you determine what type of software and tools that you need.
Functionality, does it meet your goals, can it generate the reports that you need, how easy does it do it? Example of easy of use, how many times do I need to enter data? Pricing model, does it fit your budget, is it per a month, based on number of items? Is the company more focused on software or consulting? How much support will you get?
Is there a hardware component, do you need a scanner, barcode printer, can the hardware and software interact well, you don’t want to have a scanner and printer that can’t communicate or with the software system.
Is there software flexible to expand easily such as if another department wants to add it or a stockroom? What’s the roll out? How do people get trained to use the software and hardware?
Launching the Chemical Inventory
Develop a chemical inventory plan (tip: make this document user friendly so it can used as a reference for new users)
Distribute and train applicable stack holders and notify of launch date. Especially in more decentralized organizations such as universities it’s important to let professors know if they should be gathering data or someone will need access to their lab.
Plan to handle existing inventory, does it need to be barcoded? Who will handle the initial data entry? It is important to have an accurate starting point and keep in mind, the time and effort it can take to get this data entered.
Implementation, what is the start date? How will incoming items be distributed and removed from the system?
Maintenance
Quality control and reconciliation to spot check data and reports for accuracy, errors will occur (item isn’t barcoded, item moved and not reported, etc.) worst case perform on an annual basis. Who does these audits, EH&S? What will be checked and what is the criteria?
Updating new locations and employees as they come and go, how are we going to migrate chemicals to a new location? How will employees enter and exit the inventory system and who is responsible for that transition?
We’ve talked with hundreds of labs about their inventory needs and even built a software solution called Lab Spend, we’d be happy to give you a demo.