Benefits of an Integrated Procurement and Inventory System
Integrating your procurement, inventory and safety data sheets (SDSs) management systems offers significant advantages over using separate, discrete systems. In this post we highlight the reasons and how using Lab Spend increase lab efficency.
Lab Spend is an integrated system which begins by requesting a product at the top of the work cycle shown in the figure below:
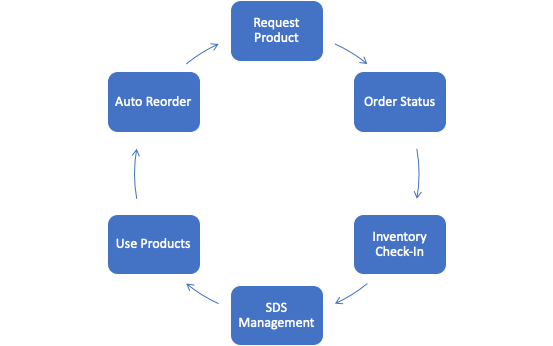
From the first step of Request Product, Lab Spend begins auto-completing data to save you time (more details here). The centralized dashboard allows all members to view requests and orders. Once an item is received, it is placed into your inventory. SDS files can be attached to each item in your inventory keeping the system in sync. Products are used and once depleted, a simple click requests the product again.
The figure below shows examples of different discrete systems that research labs use prior to implementing an integrated system:
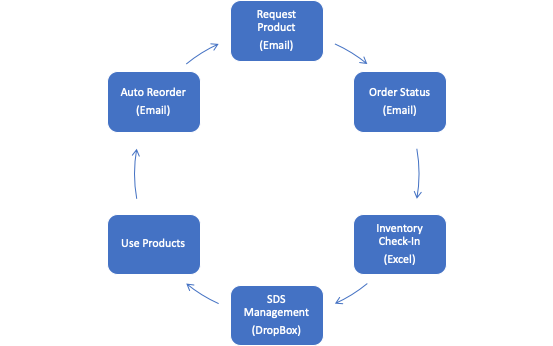
Biotechnology companies using discrete systems require a manual process to move data between systems since they’re not designed to work together.
The manual process of emailing updates costs time and communication such as status updates is often implemented inconsistently. For example, a lab manager may be trying to keep track of hundreds of items with various status (back-ordered, returned, item missing, item damaged, etc.) and then trying to communicate that to dozens of researchers is a difficult system to maintain. Often the lab manager is unable to monitor theses status and is only able to provide updates when requested by researchers. If a researcher is requesting an update is inefficient and if there is a problem it can be difficult to correct quickly such as being made aware that a critical product will be arriving weeks later than expected.
Moving along in the cycle once an item arrives it is placed into the inventory system often Excel. Since Excel doesn’t easily handle file storage, labs may use a shared DropBox folder for their SDSs, but these two systems don’t automatically synchronize causing them to drift apart over time. Since the inventory and SDSs drift apart it causes inaccuracies making the lab at risk for safety violations.
In Summary:
Integrated Lab Management Systems:
- Synchronized data
- Reduced data entry, therefore, reducing errors
- A seamless transition between placing Product Requests, Orders, Status Updates, Receiving into Inventory, and re-Ordering
- Specialized notifications and emails such as for low stock levels, service reminders or chemical expirations
Discrete Lab Management Systems:
- Labor-intensive processes
- Hard to manage through email
- No synchronization between systems
- Increased safety violations due to management difficulty
- Increasing the requirement for manual inventory checks
- Time-consuming to determine if all SDSs are on site