Inventory Monitoring for Bio-incubators and Accelerators
The landscape of research and development is rapidly changing. A relatively new concept are biotechnology incubators and accelerators. These facilities help usually smaller companies by providing lab space (more incubator) and services (more accelerator like). Bio-incubators play a critical role in supporting entrepreneurs who are developing new technology.
A bio-tech incubator has tenants that are small companies who order supplies that are needed for their research. A small biotechnology company may order 25 to 100 items per a month depending where they are in their purchasing cycle and type of research. If an incubator has 15 companies then they are looking 375 to 1,500 scientific supplies and chemicals entering the facility. Incubators have the challenge of being required to know when, what and how much of a product, which are often chemicals are being stored in their facility.
How do facilities best monitor and tracking the hundreds of items that are entering their buildings?
A problem with hundreds of items entering a facility isn’t new and is very similar to how university research labs function. A give science department may have fifteen professors who are each ordering items that enter a building. The solution that universities often use, is to hire a facilities manager often with a background in environment health and safety to assist labs with governmental compliance. For example, ensuring that labs have safety data sheets (SDSs) for the chemicals in their lab. The person may also review and maintain eye wash stations, trip hazards and help with waste management. However, hiring a dedicated facility manager is impractical with the budgets of many incubators. One solution has been to bring in a consultant to help set up systems that can then be run by the incubator staff. Another solution, which we have found more common is the owner of the facility hope all the tenants are compliant with rules and regulations without any monitoring. The scary part is that the facility itself could be held liable for fines such as by OSHA based on tenants actions. Of course, more importantly, there can be a significant safety risks such as storing in aggregate excessive volumes of flammable materials could pose to everyone in the facility. This scenario could happen if, for example, three companies are ordering ethanol and no one is monitoring of the total combined volume across the companies.
What solutions should biotech incubators consider?
To help, we at Lab Spend, have developed a facilities inventory feature. The software allows each research lab to monitor their own inventory providing an easy method to enter the chemical details, quantity, volumes and upload SDSs. This is important since compliance is more than having SDSs which is all that some incubators monitor. For example, there are specific regulations in Massachusetts where we are based about total flammable volumes within a facility and even by floor. Lab Spend allows you to easily combine volumes from multiple tenants and create customized exports.
The image below shows the dashboard of the items that are stored in the facility. The items can be refined by type such as if they are a chemical and filtered by locations and company.
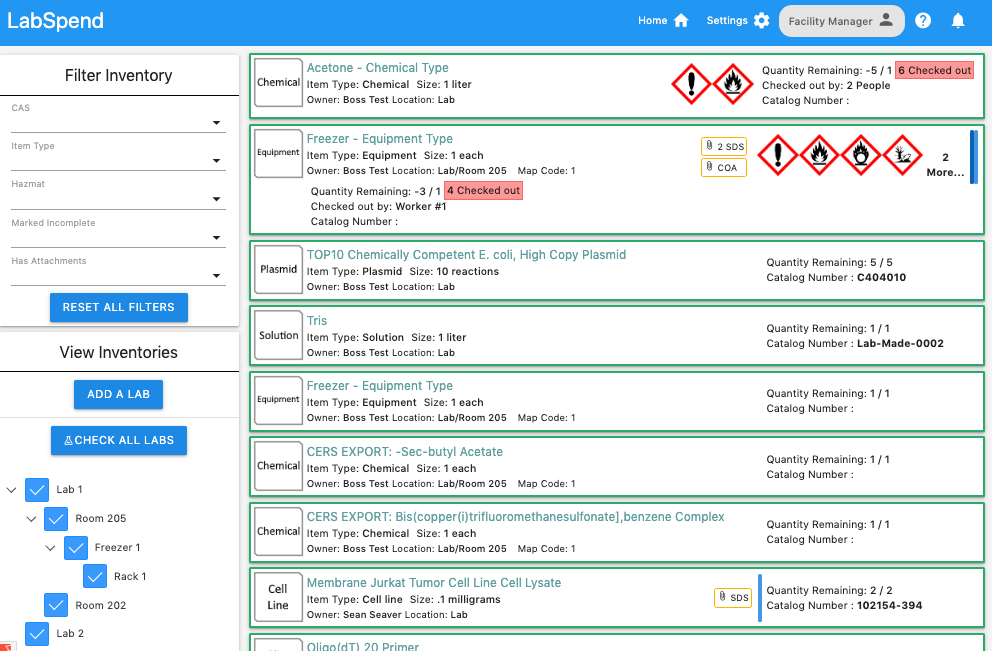
The facility lab inventory feature should be viewed as a tool to help make the process of monitoring and reporting research supplies and chemicals. Those that manage incubator spaces will still need to monitor the system, for example, a tenant my forget to enter a chemical. However, Lab Spend is a massive improvement from the nearly impossible task of accurately monitoring items manually.